The Sakura Factory (Sakura City, Chiba Prefecture), which has been in operation since 1986, produces semiconductor test sockets and various connectors. As of July 2023, we are constructing the Sakura Factory Building No.2 (tentative name) in order to further strengthen production.
In this column, we will introduce the Sakura Factory, which has received various external certifications, and which has been working on the Business Continuity Plan(BCP)*1, environmental consideration, demand response*2, etc.
To reduce CO2 emissions:
Incorporating natural energy and battery storage systems
In the past, the Sakura Factory relied on purchasing 100% of its electricity from electric power companies.
In October 2020, we installed solar power generation equipment and NAS batteries*3 that solve the difference in power demand between day and night in order to reduce the CO2 generated by purchasing power. We have adopted a system that stores surplus solar power in the NAS battery during the day and discharges and uses it at night.
As a result of the implementation of the system, the ratio of renewable energy to the amount of electricity used at the Sakura Factory is around 20%, reducing CO₂ emissions by approximately 350 tons annually. As of July 2023, the Sakura Factory has installed 445W x 1,530 solar power generation facilities.
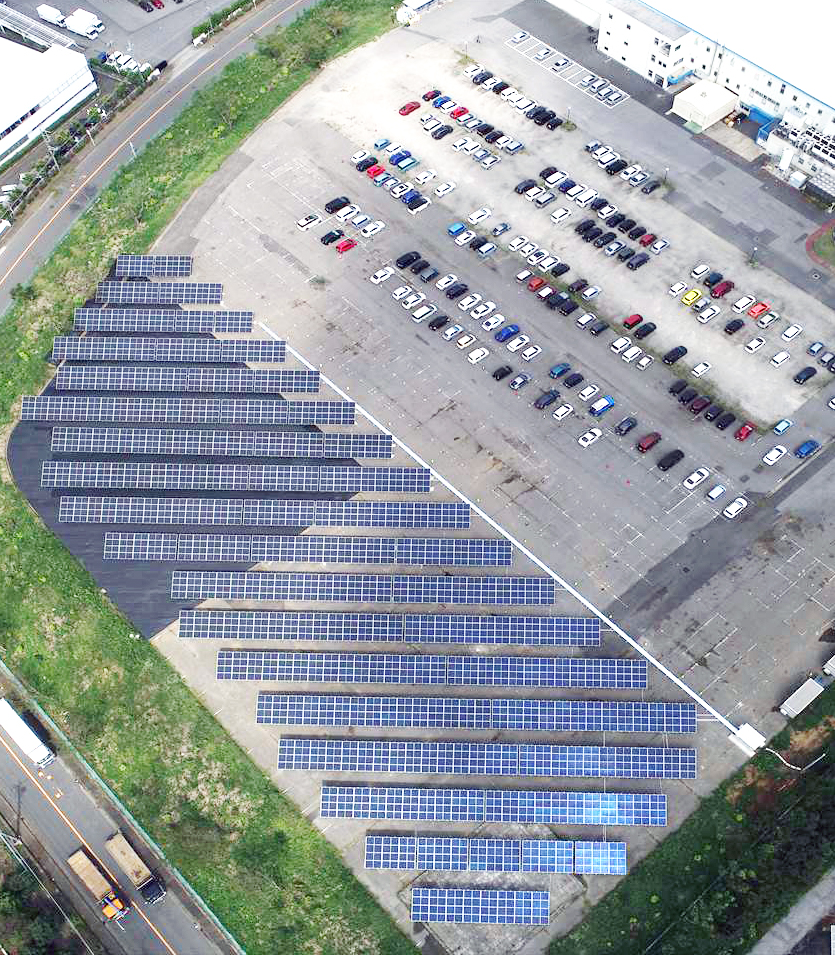
In March 2021, we concluded an agreement with Sakura City about temporary use of facility at the time of disaster. In the event of a disaster, we will open our Sakura Factory as a local evacuation center. We will also provide stockpiles of food, drinking water, blankets, and other supplies, as well as electricity for cell phones, electric vehicles, and electric motorcycles. Where is planned to be an evacuation center, can be maintained 24 hours a day, 365 days a year, including elevators, even in the event of a long lasting disaster.
In preparation for power outages, a certain amount of NAS battery capacity is left and a system is in place that can be used as an emergency power source.
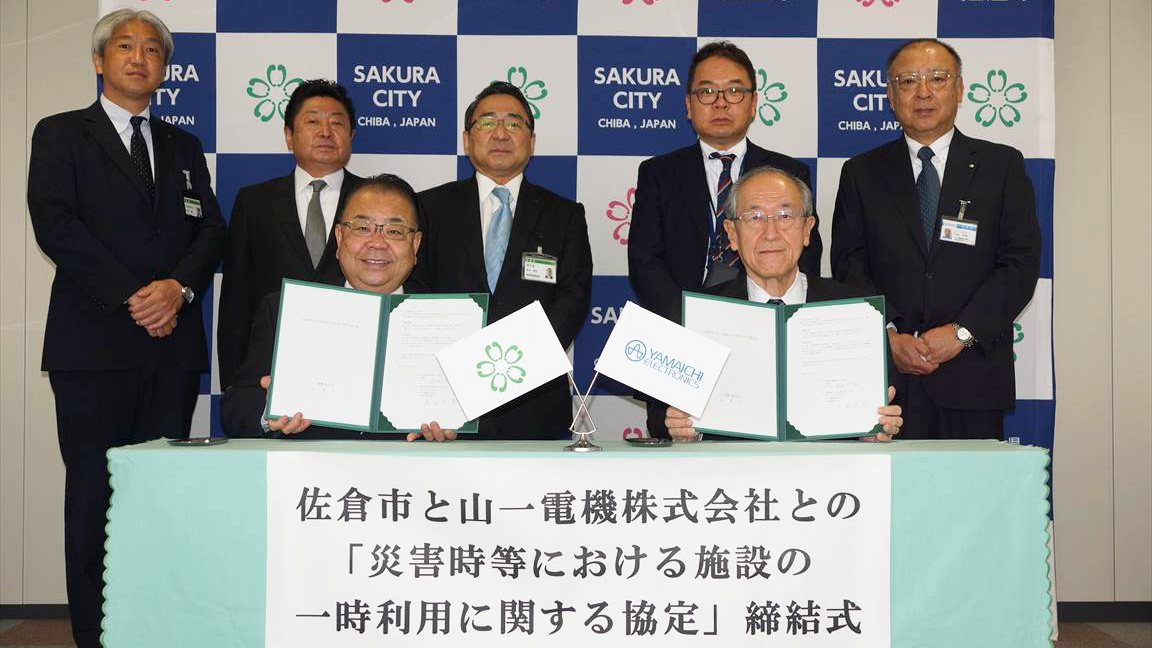
Our demand response
In recent years, power companies have been requesting power saving in the summer due to the rising demand for electricity. At the Sakura Factory, when the supply and demand for electricity becomes tight and demand response is activated, the amount of power purchased is reduced by discharging the power from the NAS battery.
By reducing the amount of electricity purchased for a few hours at the Sakura Factory, we can simultaneously save the electricity consumed by hundreds of ordinary households. In addition, we are contributing to improving the power supply and demand balance in the city by delaying the operating hours of equipment that consumes a large amount of power as long as it does not interfere with production activities.
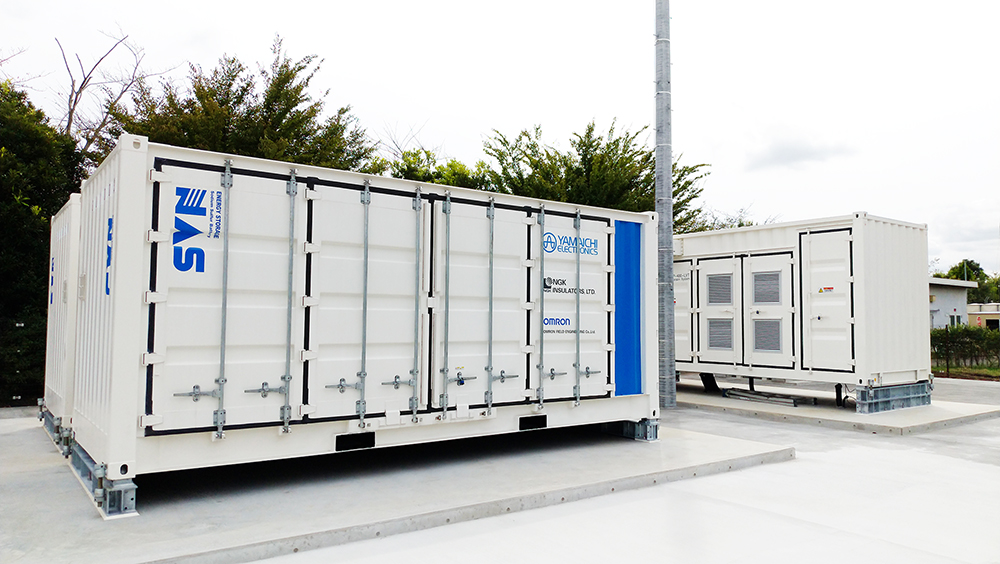
Acquired the highest S class in the evaluation system
by the METI
From the fiscal year of 2016, the business operator classification evaluation system began in Japan, in which all business operators who submit regular reports under the Energy Conservation Law are classified into four levels: S, A, B, and C. As a result of efforts such as updating aging air conditioning equipment to high-efficiency air conditioning equipment, switching to LED lighting, and reducing power consumption by visualizing power consumption, Yamaichi Electronics achieved the highest S class in the fiscal year of 2021 and 2022.
The Sakura Factory Building No.2
received the highest BELS ranking of 5 stars
The Sakura Factory Building No.2 received the highest rank out of 5 in the Building Energy-efficiency Labeling System (BELS*4), and acquired the “ZEB*5 Ready” certification.
We plan to install photovoltaic power generation equipment on 63% of the roof area of the Sakura Factory Building No.2, which is expected to reduce CO2 emissions by approximately 180 tons per year compared to when power is purchased from a power company.
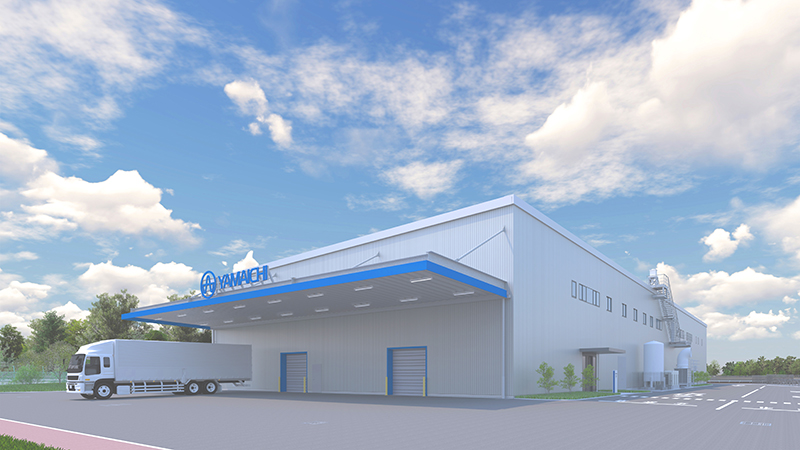
The future we aim for
Yamaichi Electronics aims to reduce energy consumption by an average of 1% annually based on the activities specified in ISO14001, and aims to improve by 5% or more by the end of FY2024, based on FY2019. We will continue to strengthen the production of electronic components and contribute to the realization of a prosperous society by conducting production and development that considers the global environment.
*1 Business Continuity Plan(BCP): In the event of a major natural disaster, infectious disease, or other business continuity risk, this refers to a plan that outlines methods and systems to minimize damage and restore operations in the shortest possible time. Yamaichi Electronics has established a code of conduct in preparation for emergencies such as large-scale natural disasters. And in the event of a disaster, we will of course give top priority to the safety and security of our employees and will work to continue our business.
*2 demand response: It is a mechanism that adjusts the balance of power supply and demand by having consumers control the amount of power used when there is a risk that the balance between power supply and demand will be disrupted due to extreme heat.
*3 The NAS battery: The system was developed as a means of resolving the disparity in electricity demand between day and night, and can store and discharge electricity.
*4 BELS:BELS stands for Building-Housing Energy-efficiency Labeling System. This is an indication system for the energy efficiency performance of buildings, which was started in 2014 by the Association for Housing Performance Evaluation and Labeling. A BEI (Energy Saving Performance Index) value is calculated, and a 5-star rating is given based on that value. Furthermore, buildings with excellent energy-saving performance are certified as ZEB.
*5 ZEB:ZEB stands for Net Zero Energy Building. It is a building that aims to achieve zero energy balance by introducing renewable energy after reducing primary energy consumption through energy-saving measures. Among the definitions, “ZEB Ready” refers to buildings that have reduced standard primary energy consumption by 50% or more through energy conservation.